Sheet metal fabrication plays a vital role across multiple industries, including automotive, aerospace, construction, and electronics. Selecting the appropriate sheet metal is essential to achieving durability, cost efficiency, and seamless production. Several factors influence the choice of sheet metal materials, such as strength, corrosion resistance, and workability. Understanding these elements helps manufacturers make informed decisions, ensuring the final product meets both functional and aesthetic requirements.
This blog delves into the five key factors that should be considered when selecting sheet metal fabrication.
What is Sheet metal fabrication?
Sheet metal fabrication refers to thin, flat pieces of metal that are used as the primary material for creating various products through a manufacturing process called sheet metal fabrication. This process involves cutting, bending, shaping, and assembling the metal into a desired form or structure, often through techniques like welding, stamping, or laser cutting.
Sheet metal is commonly made from various types of metals, including steel, aluminum, stainless steel, copper, and brass, each offering specific benefits depending on the intended application.
In sheet metal fabrication, the material is typically purchased in standard thicknesses and can be customized to suit specific project needs. It’s widely used in industries such as construction, automotive, aerospace, and electronics, due to its versatility, strength, and cost-effectiveness.
Key features of sheet metal include :
- Flexibility : Can be formed into complex shapes with precision.
- Durability : Especially with metals like stainless steel, sheet metal is highly resistant to wear and corrosion.
- Lightweight : Metals like aluminum are light, yet strong, making them ideal for certain applications.
- Cost-effective : Compared to solid metal pieces, sheet metal can be more economical, especially for large scale production.
5 reason for Choosing Sheet Metal Fabrication
1. Material Type and Properties
The first and foremost factor to consider when choosing sheet metal fabrication is the material type. Different metals have varying properties, which can affect the final product’s strength, weight, corrosion resistance, and overall performance. Here are some common sheet metal types :
Metal Type | Characteristics | Common Applications |
Steel | Strong, Durable, Corrosion-resistant |
Construction, Automotive, Industrial equipment |
Aluminum | Lightweight, Corrosion-resistant, Good conductivity |
Aerospace, Electronics, Consumer products |
Stainless Steel | High corrosion resistance, Durable |
Medical equipment, Food processing, Architecture |
Copper | Excellent conductivity, Corrosion-resistant |
Electrical components, Roofing, Plumbing |
Brass | Malleable, Good corrosion resistance |
Decorative elements, Fittings, Musical instruments |
2. Thickness of the Metal
The thickness of the sheet metal is another crucial factor that influences both the fabrication process and the final product’s performance. Sheet metal comes in various thicknesses, typically measured in gauge (with lower numbers representing thicker metals).
- Thin Sheet Metal (24-28 gauge) : Thin sheet metals are easier to cut, bend, and shape. They are typically used for applications that require lighter components, such as appliances, electronic enclosures, and decorative items.
- Medium Thickness (18-22 gauge) : These gauges are ideal for general-purpose applications, such as automotive parts, HVAC systems, and building materials. This thickness provides a balance between strength and ease of fabrication.
- Thick Sheet Metal (10-16 gauge) : Thicker sheet metals are used for heavy-duty applications where strength and durability are paramount, such as structural components, industrial machinery, and pressure vessels.
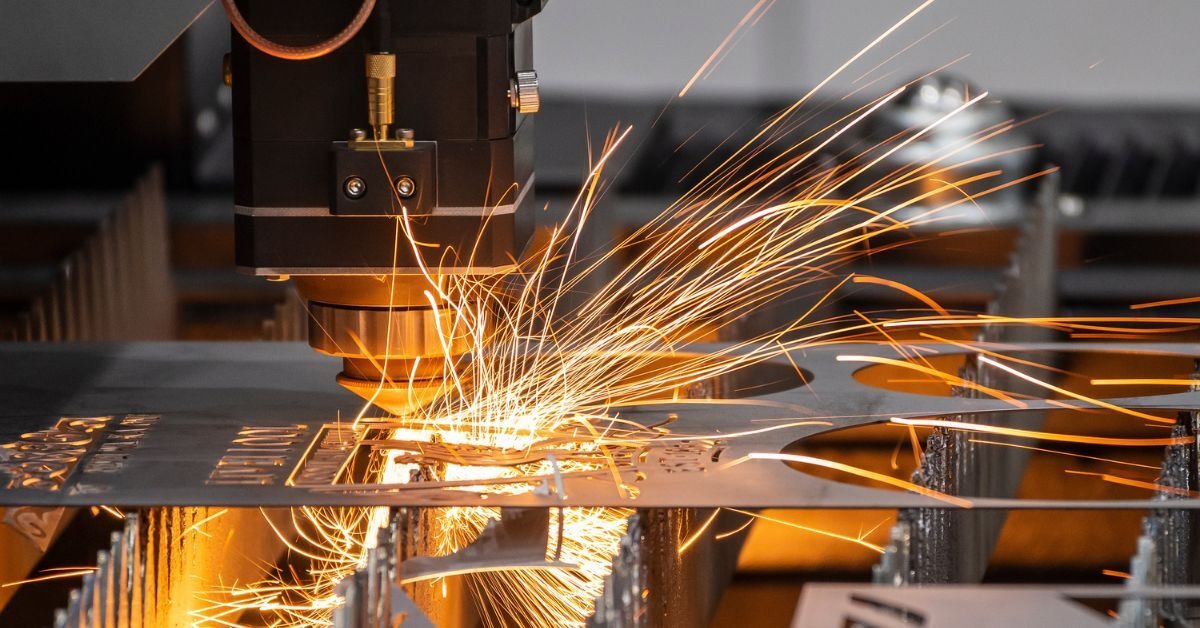
Note : It’s important to choose the right thickness to ensure that the material can handle the stresses it will encounter during its service life. Too thin a material might lead to failure under pressure, while too thick a material might make the fabrication process more difficult and costly.
3. Formability and workability
Formability and workability are crucial aspects of sheet metal fabrication, influencing how easily a metal can be shaped, bent, or stretched without breaking. Various techniques such as bending, stamping, deep drawing, and roll forming are employed to shape metal sheets. The ductility of a material, such as aluminum and copper, makes it easier to manipulate, while harder metals like stainless steel require more force and advanced machinery.
Additionally, the elongation rate of a metal determines its stretchability, which is essential for deep drawing applications. Selecting a material with good formability and workability ensures smooth production, minimizes defects, and enhances the overall efficiency of the fabrication process.
4. Corrosion Resistance and Environmental Factors
Corrosion resistance is vital in applications exposed to moisture, chemicals, or extreme temperatures. Some metals, such as stainless steel and aluminum, naturally resist corrosion due to their chemical composition, while others, like mild steel, require coatings or treatments to enhance their longevity. Surface finishing options, such as powder coating, anodizing, and electroplating, not only improve corrosion resistance but also enhance the aesthetic appeal of the final product. Galvanized steel, for example, is coated with zinc to prevent rusting, while anodizing is commonly used for aluminum to provide a durable, decorative finish.
Before deciding on the material for your sheet metal fabrication, assess the environmental conditions the product will be exposed to. If the product will be used outdoors or in high-humidity areas, choosing a material with strong corrosion resistance will save on long-term maintenance costs and increase the product’s lifespan.
5. Cost and Budget Considerations
While selecting the right material for sheet metal fabrication is important for the quality of the final product, cost is often a determining factor in material selection. Different metals vary widely in price, and sheet metal fabrication costs can quickly add up depending on the material you choose.
- Steel : Steel is typically more affordable than other metals, making it a go-to choice for many industries. Carbon steel is generally cheaper than stainless steel, so if cost is a major factor in your project, carbon steel might be the best choice.
- Aluminum : Aluminum tends to be more expensive than steel, but it can still be cost-effective when you factor in its lightweight properties, corrosion resistance, and ease of handling. For high-performance projects, aluminum can offer a great balance between cost and benefits.
- Copper and Brass : These metals are generally more expensive due to their manufacturing processes and unique properties. They’re typically used in specialized applications where their performance justifies the higher cost.
When choosing sheet metal fabrication, always consider your project’s budget constraints and balance cost against performance. A more expensive material may offer superior benefits, but only if those benefits are necessary for your project’s requirements.
The Only Solution for Sheet Metal Fabrication
When it comes to precision sheet metal fabrication,we are the only solution you need. We specialize in delivering custom, high-quality metal components with advanced fabrication techniques and expert craftsmanship. From cutting and bending to welding and finishing, we handle every step with efficiency, accuracy, and reliability.
With years of experience and a commitment to excellence, we provide cost-effective, durable, and innovative solutions for businesses across India. No matter the complexity of your project, we ensures on-time delivery and superior quality—every time.For professional sheet metal fabrication solutions, reach out to us at 📞+91 9148785173, email 📧 sales@hanav.in or visit 🌐 HanaV.in.
Conclusion
Choosing the right sheet metal fabrication with HanaV is a great decision that can impact the strength, durability, performance, and cost-effectiveness of your project. By considering factors such as material type, thickness, corrosion resistance, fabrication method, and cost, you can make an informed decision that meets both your technical and financial requirements.
Whether you’re working with stainless steel, aluminum, or carbon steel, always take the time to assess your project’s specific needs and choose the material that best aligns with those needs. With the right sheet metal, your fabrication process will go smoothly, and your final product will stand the test of time.