In the world of metal manufacturing, casting and machining go hand in hand to create high-quality, precision-manufacturing metal parts. This combination provides a balance of cost-effectiveness, accuracy, and durability, making it the preferred choice for industries such as automotive, aerospace, construction, and heavy machinery.
While casting forms the basic shape of a metal part, machining enhances its accuracy, surface finish, and functional performance. When combined, these processes result in superior mechanical properties, tighter tolerances, and a highly efficient production cycle.
In this blog, we’ll explore why casting and machining are a perfect combination, the benefits they offer, and how HanaV delivers precision manufacturing metal components with these advanced manufacturing techniques.
What is Casting?
Casting is a manufacturing process where molten metal is poured into a predefined mold and allowed to solidify into the desired shape. This method is ideal for producing complex metal components with minimal material waste. Various casting techniques are used based on the required properties and applications.
Types of Casting Methods
Casting Method | Description | Common Applications |
Sand Casting | Utilizes a sand mold for shaping and producing metal components. | Engine blocks, pump housings |
Die Casting | Injects molten metal into a steel mold under pressure | Automotive parts, aerospace components |
Investment Casting | Uses wax patterns for high-precision metal parts | Medical devices, turbine blades |
Centrifugal Casting | Uses rotational force to distribute molten metal | Pipes, cylinder liners |
Continuous Casting | Produces long metal sections by solidifying metal continuously | Bars, rods, sheets |
Each method has its own advantages, depending on factors like material type, required strength, complexity, and production volume.
What is Machining?
Once the casting process is complete, the raw metal part often requires additional precision and finishing. This is where machining comes in.
Machining is a subtractive manufacturing process that removes excess material from a workpiece to achieve precise dimensions, shapes, and surface finishes. The process is carried out using CNC (Computer Numerical Control) machines, lathes, milling machines, and grinding tools.
Types of Machining Processes
Machining is a crucial manufacturing process that enhances the accuracy, functionality, and surface quality of metal components. Various machining techniques are used to shape, cut, and refine cast metal parts, ensuring they meet exact specifications. Below are some key machining processes :
- CNC Machining – A highly precise and automated process that uses computer-controlled tools to cut, shape, and finish metal components. CNC machining ensures consistent quality, tight tolerances, and complex geometries, making it ideal for high-precision applications in industries like aerospace, automotive, and medical equipment.
- Turning – A subtractive process in which the metal workpiece rotates while a stationary cutting tool removes material. This method is commonly used to create cylindrical parts, such as shafts, rods, and bushings, ensuring smooth finishes and precise diameters.
- Milling – Uses rotary cutters to remove material from a stationary workpiece, allowing for the creation of intricate shapes, slots, and contours. Milling is versatile and widely used in manufacturing components with complex geometries and high structural integrity.
- Grinding – A finishing process that enhances surface smoothness and dimensional accuracy by removing small amounts of material with an abrasive wheel. Grinding ensures excellent surface finishes and is essential for achieving high tolerances in precision parts.
- Drilling – A fundamental machining process that creates precise holes using rotating drill bits. It is used in nearly every manufacturing industry, ensuring accuracy in hole placement and size, which is critical for assembly and fastener applications.
Why is Casting and Machining a Perfect Combination?
Combining casting and machining ensures that metal components meet the highest standards of quality, performance, and durability. These two manufacturing processes complement each other, providing cost-effective, high-precision, and high-strength parts. By leveraging the advantages of both processes, industries can improve product consistency, reduce waste, and enhance efficiency.
1. Cost-Effectiveness and Material Efficiency
Casting helps create near-net shape components, significantly reducing the amount of machining required. This leads to a reduction in raw material costs, especially for expensive metals and alloys like titanium, aluminum, stainless steel, and brass. Less material waste not only results in cost savings but also improves sustainability in metal fabrication industries by reducing excess scrap.
Additionally, the ability to produce multiple parts in a single casting process helps manufacturers save time and labor costs. With proper design optimization, casting minimizes excess machining, reducing wear and tear on CNC machines and extending their lifespan.
2. Achieving Complex Geometries
Casting enables the production of intricate shapes and internal structures that would be difficult, time-consuming, or costly to achieve through CNC machining alone. This includes hollow sections, undercuts, and intricate patterns.
Precision machining then refines these shapes by adding fine details, precise dimensions, and specific tolerances, ensuring the final product meets exact specifications. This process is widely used in industries such as automotive, aerospace, and industrial manufacturing, where complex metal components are required to function optimally in high-performance environments.

3. Enhanced Dimensional Accuracy
Casting alone may result in minor inaccuracies due to shrinkage, cooling effects, or mold inconsistencies. While advanced casting methods help control these deviations, CNC machining ensures tight tolerances, producing precision parts that fit perfectly within an assembly.
This is particularly critical for engine components, aircraft parts, and medical devices, where precision and reliability are crucial. Using machining as a secondary process after casting guarantees dimensional stability and product consistency, preventing issues such as misalignment or improper fitting.
4. Superior Surface Finish
Raw cast parts may have rough surfaces, seams, or minor imperfections due to the molding process. These imperfections can affect both functionality and aesthetics. Machining smooths out these surfaces, improving both the appearance and mechanical properties of the component.
A high-quality surface finish is essential in applications where friction, corrosion resistance, or hygiene standards are critical, such as in aerospace, medical, and food processing industries. The combination of casting and machining allows manufacturers to deliver products with a polished, defect-free, and high-performance finish.
5. Stronger and More Durable Parts
Casting forms a solid base structure, ensuring good strength and integrity. The casting process allows for the use of specialized heat treatment techniques, enhancing material properties such as hardness, toughness, and corrosion resistance.
However, raw cast parts can sometimes develop porosity, internal defects, or inconsistent grain structures. Machining eliminates these defects, ensuring superior mechanical performance, uniform strength distribution, and long-term durability.
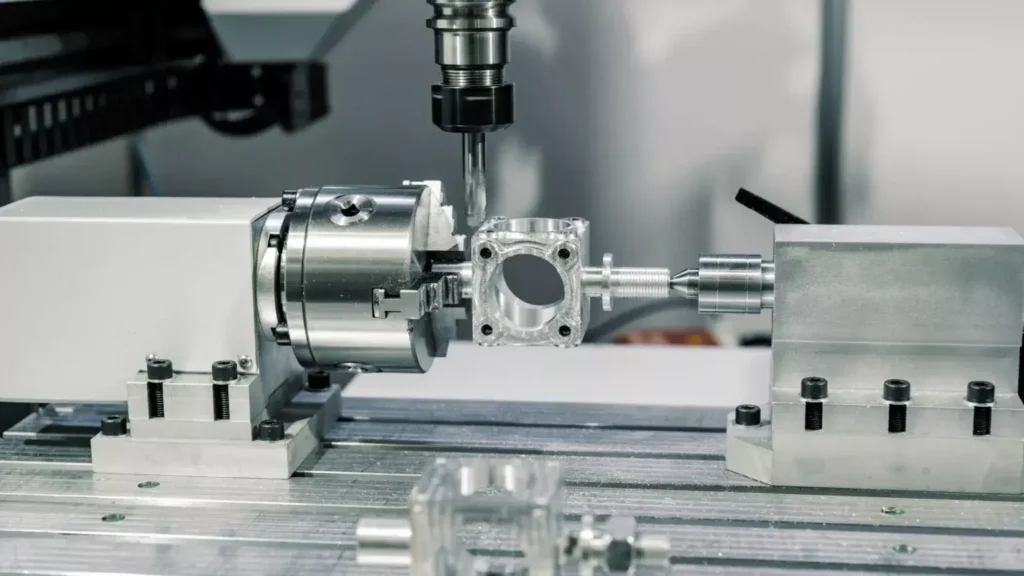
Industries such as oil & gas, defense, construction, and industrial machinery manufacturing rely on this process combination to produce robust, load-bearing components that can withstand extreme pressures, high temperatures, and harsh working conditions.
6. Faster Production and Scalability
Casting speeds up the bulk production of rough parts, reducing overall lead times and ensuring that manufacturers can produce components in high volumes. This method is particularly beneficial for mass production of standardized parts.
Once the cast parts are produced, CNC machining finalizes them with extreme accuracy, ensuring uniformity across multiple pieces. This process combination is perfect for industries requiring large-scale manufacturing while maintaining high precision and quality standards.
Additionally, with automation and advanced CNC technology, machining can be efficiently scaled for both custom and high-volume production, ensuring manufacturers meet market demand without sacrificing precision.
Industries That Benefit from Casting and Machining
Many industries rely on the combination of casting and machining for producing critical metal components :
- Automotive Industry – Engine blocks, transmission housings, brake system components.
- Aerospace & Defense – Components for aircraft engines, landing gear assemblies, and military-grade structures.
- Industrial Machinery – Heavy-duty machine components, hydraulic parts.
- Medical Equipment – Surgical tools, prosthetic implants.
- Defense and Military – Weapon parts, armored vehicle components.
- Oil and Gas – Pipeline fittings, drilling equipment.
Why Choose HanaV for Casting and Machining?
At HanaV, we specialize in precision casting and CNC machining, offering end-to-end solutions for high-quality metal parts. Our state-of-the-art manufacturing facility and experienced engineers ensure that every component meets the highest industry standards.
Why Partner with HanaV?
- ISO-certified manufacturing processes
- Expertise in CNC machining and metal casting
- Custom metal parts with precision tolerances
- Cost-effective and efficient production
- Rapid prototyping and high-volume manufacturing
- On-time delivery with reliable supply chain management
We cater to industries such as automotive, aerospace, medical, industrial, and defense, providing high-performance metal parts tailored to your needs.
Conclusion
Casting and machining work together as the perfect combination for producing durable, precise, and cost-effective metal parts. While casting creates the basic structure, machining enhances accuracy, surface quality, and functionality. This combination is crucial for industries that require high-performance metal components.
If you’re looking for expert casting and machining services, HanaV is your trusted partner for precision manufacturing solutions.
📧 Email : sales@hanav.in
🌍 Website : www.hanav.in
📞 Phone : +91 9148785173 Contact us today to discuss your custom metal component needs and experience world-class manufacturing excellence!